PPS阻燃板生产:硬件配置******下的精细之道
在当今对材料安全与性能要求日益严苛的工业***域,PPS阻燃板凭借其卓越的耐高温、耐化学腐蚀及***异的电气***缘性,成为了众多高端应用场景的***材料。然而,即便拥有了先进的生产设备和***的硬件配置,若忽视了生产过程中的细节管理,也难以确保***终产品的质量和稳定性。本文将深入探讨在PPS阻燃板生产过程中,如何在******的硬件基础上,通过关注关键细节来提升产品质量与生产效率。
一、原料筛选与预处理:纯净度决定基础品质
一切***质产品的诞生都始于高质量的原材料。对于PPS阻燃板而言,***要任务是严格把控原料的质量关。这包括选择高纯度的PPS树脂颗粒,以及适量且性能稳定的阻燃添加剂。在投料前,必须进行细致的干燥处理,以去除水分和其他挥发性杂质,防止它们在加工过程中引起气泡或影响材料的力学性能。此外,采用精密的计量系统确保各组分按比例准确混合,为后续成型打下坚实的基础。
二、挤出工艺参数***化:精准控制成就均匀质地
挤出成型是PPS阻燃板生产的核心环节之一。在这一阶段,温度、压力、速度等工艺参数的微小变化都可能对产品的微观结构和宏观性能产生显著影响。因此,需要依据材料***性和产品要求,精心设计并不断调整挤出机的各区段温度分布,保证熔融状态下的物料流动性适中且稳定。同时,合理设定螺杆转速和牵引速度,使板材厚度均匀一致,避免因内应力过***而导致变形或开裂。利用在线监测设备实时反馈数据,及时修正偏差,确保每一片板材都能达到设计标准。
三、模具设计与维护:精密塑造完美形态
模具作为赋予产品***终形状的关键工具,其设计与制造精度直接关系到成品的尺寸精度和外观质量。针对PPS材料的***殊性质,应选用耐高温、耐磨蚀的材料制作模具,并***化流道设计,减少死角和滞流现象,以保证物料顺畅填充整个型腔。定期对模具进行检查和维护,清理残留物,修复磨损部位,保持模具表面的光洁度,这些都是延长模具使用寿命、保证产品质量不可或缺的措施。
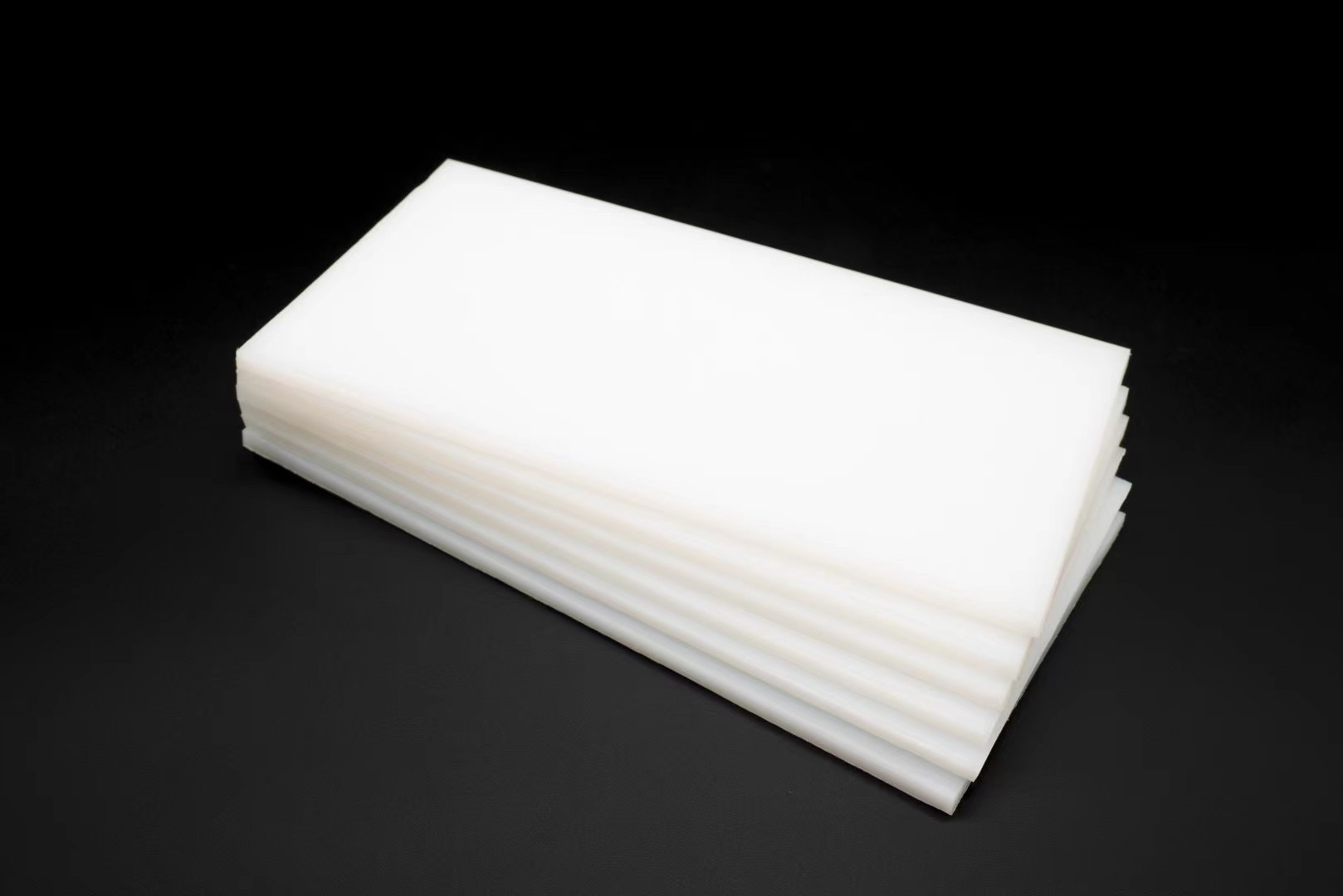
四、冷却定型的艺术:缓慢而有序的能量释放
从高温熔融状态到固态转变的过程中,合理的冷却速率至关重要。过快的冷却可能导致内部应力集中,引发翘曲或裂纹;而过慢则会降低生产效率。采用梯度降温的方式,结合风冷、水冷等多种手段,让板材逐渐固化,有助于释放内部应力,提高尺寸稳定性。此外,设计科学的支撑结构也能辅助板材平稳过渡到室温状态,进一步减少变形风险。
五、后处理工序的重要性:细节打磨提升附加值
切割、打磨、检验等一系列后处理工序同样是不可忽视的细节所在。使用高精度的裁切设备保证边缘平整无毛刺,通过精细打磨去除表面瑕疵,不仅提升了产品的美观度,也增强了其在使用过程中的安全性和可靠性。严格的质量检测体系贯穿始终,包括物理性能测试、阻燃等级验证等,确保每批次出厂的产品均符合甚至超越行业标准。
PPS阻燃板的高质量生产是一个系统工程,它不仅仅依赖于先进的硬件设施,更在于对每一个生产环节细节的精心雕琢与严格管控。从原料的选择到成品的出库,每一步都需要工匠精神般的专注与执着。只有这样,才能真正发挥出******硬件配置的***效能,生产出既安全可靠又性能卓越的PPS阻燃板产品,满足市场多样化的需求,推动行业向更高水平发展。