PPS塑料管缺陷及加工分类详解
PPS塑料管以其耐高温、耐化学腐蚀、机械性能***异等***点,在工业、化工、环保等***域应用广泛。然而,其加工过程中易出现多种缺陷,且加工方式因分类不同而有所差异。以下从缺陷分析和加工分类两方面进行详细阐述。
一、PPS塑料管的常见缺陷及原因分析
1. 耐温性不足与变色问题
缺陷表现:制品在高温环境下出现变形、变色(如黄纹、黑点)或发黑现象。
主要原因:
再生料或配混问题:使用低质回收料或不当添加阻燃剂、填充剂,导致熔点差异***,高温下材料碳化或分解。
工艺参数不当:料筒温度过高(尤其是前段)、螺杆转速过快、背压过***,导致剪切热过高,引发熔体破裂或局部灼烧。
解决方案:***化原料配比,分段控制料筒温度(如尼龙共混改性时采用260℃~310℃梯度降温),并清理料筒残留杂质。
2. 表面质量差与玻纤外露
缺陷表现:制品表面粗糙、光泽度低,玻璃纤维暴露。
主要原因:
模具温度偏低:PPS为结晶性高分子,模温过低会导致冷却过快,结晶不充分,表面固化层阻碍内部收缩,形成内应力。
模具表面光洁度不足:型腔未抛光或镀铬,直接导致制品表面质量差。
解决方案:提高模温至120℃以上,并对模具型腔进行抛光或镀铬处理。
3. 内应力导致的开裂
缺陷表现:制品内部出现微小裂缝,尤其在受热或接触溶剂时加剧。
主要原因:
取向应力:注射速率快、浇口设计不合理(如潜伏式点浇口不适用),导致分子链取向冻结。
温度应力:熔体与模温温差***,表层快速冷却形成压缩应力,内部产生拉伸应力。
解决方案:采用变速注射(先快速充模后低速保压)、***化浇口位置(如厚壁处设平浇口),并进行后处理(200℃热处理2~3小时)以消除内应力。
4. 其他常见缺陷
韧性不足与冲击强度低:未改性PPS本身延展性差,需通过共混改性(如添加尼龙)提升冲击强度。
尺寸变形:保压时间过长或冷却不均匀导致收缩率过***,需调整工艺参数。
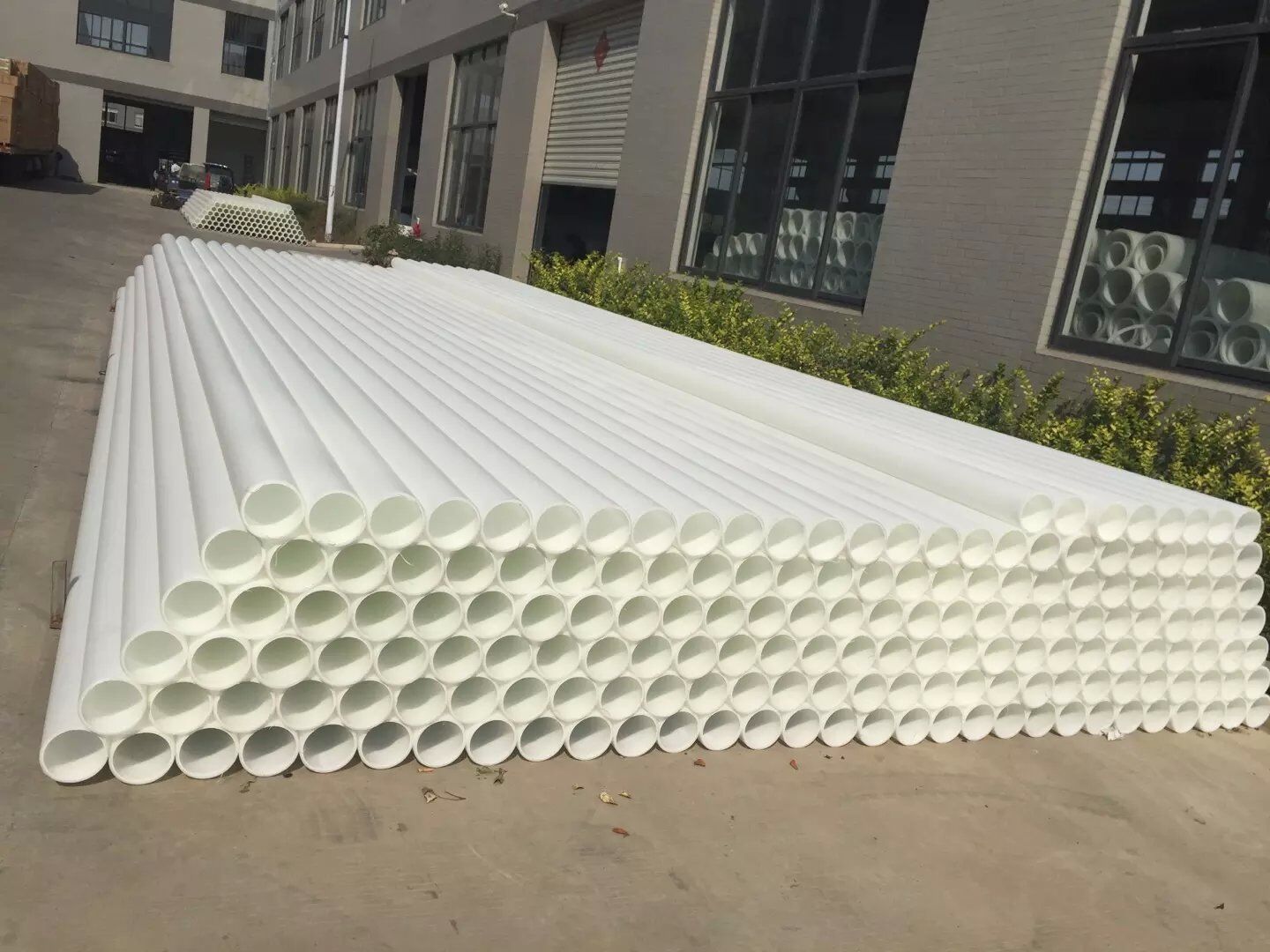
二、PPS塑料管的加工分类
PPS塑料管的加工方式因其结构、性能需求及应用场景的不同而分为多种类型,以下是主要分类:
1. 按加工工艺分类
挤出成型:
***点:适用于连续生产长管材,成本低、效率高。
适用场景:普通输水、排气管道,需控制挤出速度和冷却速率以避免变形。
缺陷对策:使用导流锥和支架***化熔体分布,避免轴向与周向强度不均。
注射成型:
***点:适合复杂形状制品,精度高,但需注意内应力控制。
适用场景:电器配件、精密零件,需后处理消除内应力。
共挤出成型:
***点:多层复合管材,内外层可分别采用不同材料(如PPS+耐磨层)。
适用场景:化工输送管、高耐腐蚀环境。
2. 按增强方式分类
玻璃纤维增强PPS管:
***点:刚性和耐热性显著提升,但易出现玻纤外露。
工艺要点:模具温度需达120℃以上,并采用低剪切速率。
填料改性PPS管:
***点:通过添加无机填料(如碳酸钙)降低成本,但可能影响韧性。
共混改性PPS管:
常见组合:PPS+尼龙(提升冲击强度)、PPS+PTFE(改善耐磨性)。
3. 按用途分类
工业输送管:耐高温高压,需玻璃纤维增强,内径光滑以降低流体阻力。
电器***缘管:注重耐电弧性和尺寸稳定性,常采用低介电损耗的共混改性材料。
环保过滤管:多孔结构,需通过发泡或烧结工艺制备,依赖精密模具设计。
三、总结与建议
PPS塑料管的缺陷多源于原料选择、工艺控制及模具设计,需通过***化温度梯度、调整注射参数、改进模具表面处理等方式解决。加工分类则需根据应用场景选择合适工艺(如挤出或注射)及改性方法(如玻纤增强或共混)。未来,通过智能化检测(如基于BP神经网络的表面缺陷识别技术)和工艺***化,可进一步提升PPS管的性能与生产效率。