PPS塑料管注塑伸缩问题的深度剖析与解决之道
在塑料制品的注塑成型***域,PPS塑料管因其卓越的性能,如耐高温、耐腐蚀、机械强度高等,被广泛应用于众多工业场景。然而,PPS塑料管在注塑过程中常常面临一个棘手的问题——伸缩问题,这不仅影响产品的尺寸精度和外观质量,还可能对产品的性能和使用寿命产生不利影响。深入理解PPS塑料管注塑伸缩问题的成因,并掌握正确的解决方法,对于提升产品质量和生产效率至关重要。
一、PPS塑料管注塑伸缩问题的根源探究
(一)材料的热膨胀与收缩***性
PPS作为一种高性能热塑性塑料,具有明显的热胀冷缩***性。在注塑成型过程中,熔融状态的PPS塑料被注入模具型腔,当温度迅速下降时,塑料会发生体积收缩。这种收缩在不同方向上可能不均匀,导致塑料管出现尺寸变化,这是伸缩问题产生的一个基本原因。例如,在厚度方向上,由于冷却速度相对较慢,可能会产生较***的收缩;而在长度方向上,如果模具设计不合理或工艺参数控制不当,也会出现明显的尺寸偏差。
(二)模具设计与制造的精度影响
1. 模具型腔尺寸精度:如果模具型腔的尺寸设计不准确,没有充分考虑PPS塑料的收缩率,那么注塑成型后的塑料管尺寸就很难达到预期要求。例如,型腔尺寸过***,会导致塑料管在冷却后尺寸偏***,出现伸缩过度的现象;反之,型腔尺寸过小,则可能使塑料管在成型过程中受到过度的挤压,产生内应力,进而在脱模后发生变形伸缩。
2. 模具结构合理性:不合理的模具结构,如浇口位置、冷却系统设计等,也会对PPS塑料管的伸缩产生影响。浇口位置不当可能导致塑料流动不均匀,在局部区域产生应力集中,从而引发伸缩变形。冷却系统如果不能保证塑料管在各个部位均匀冷却,会使不同部位的收缩率差异增***,进一步加剧伸缩问题。
(三)注塑工艺参数的敏感性
1. 温度控制:注塑过程中的熔体温度、模具温度以及环境温度对PPS塑料管的伸缩有着显著影响。熔体温度过高,会使塑料的流动性增加,但同时也可能导致塑料分解产生气体,在冷却时形成气泡或使塑料管内部产生空洞,从而影响其尺寸稳定性;熔体温度过低,则会造成塑料流动性差,填充不满型腔,或者在填充过程中产生较***的剪切力,导致分子取向不均匀,增加伸缩的可能性。模具温度的控制同样关键,合适的模具温度有助于塑料均匀冷却,减少收缩率的差异。如果模具温度过高,塑料管脱模后会因冷却收缩过***而产生伸缩变形;模具温度过低,则会使塑料过早冷却,在型腔内形成较***的应力,脱模后也容易出现伸缩问题。此外,环境温度的变化也会对注塑过程产生影响,尤其是在温度波动较***的生产环境中,如果没有对注塑机和模具进行有效的温度调节,很容易导致塑料管的尺寸不稳定。
2. 压力控制:注塑压力和保压压力的设置直接影响塑料管的成型质量和伸缩情况。注塑压力过低,塑料无法充分填充型腔,会导致塑料管壁厚不均匀,在冷却时产生不均匀收缩,进而引起伸缩变形。保压压力不足或保压时间过短,会使塑料在冷却过程中出现倒流现象,在塑料管内部形成缩孔或表面凹陷,同时也会影响尺寸精度,导致伸缩问题。而注塑压力和保压压力过高,则会使塑料管内部产生较***的残余应力,在脱模后应力释放,造成伸缩变形。
3. 注射速度和时间:注射速度过快,会使塑料在型腔内产生湍流和剪切应力,导致分子取向程度增加,在冷却时由于分子链的取向收缩,会使塑料管在不同方向上的收缩率差异增***,从而产生伸缩变形。注射速度过慢,则会使塑料在充模过程中过早冷却,无法完全填满型腔,或者在填充过程中形成熔接痕,这些都会削弱塑料管的结构强度,增加伸缩的可能性。注射时间的长短也需要***控制,过长或过短的注射时间都可能影响塑料管的成型质量和尺寸稳定性。
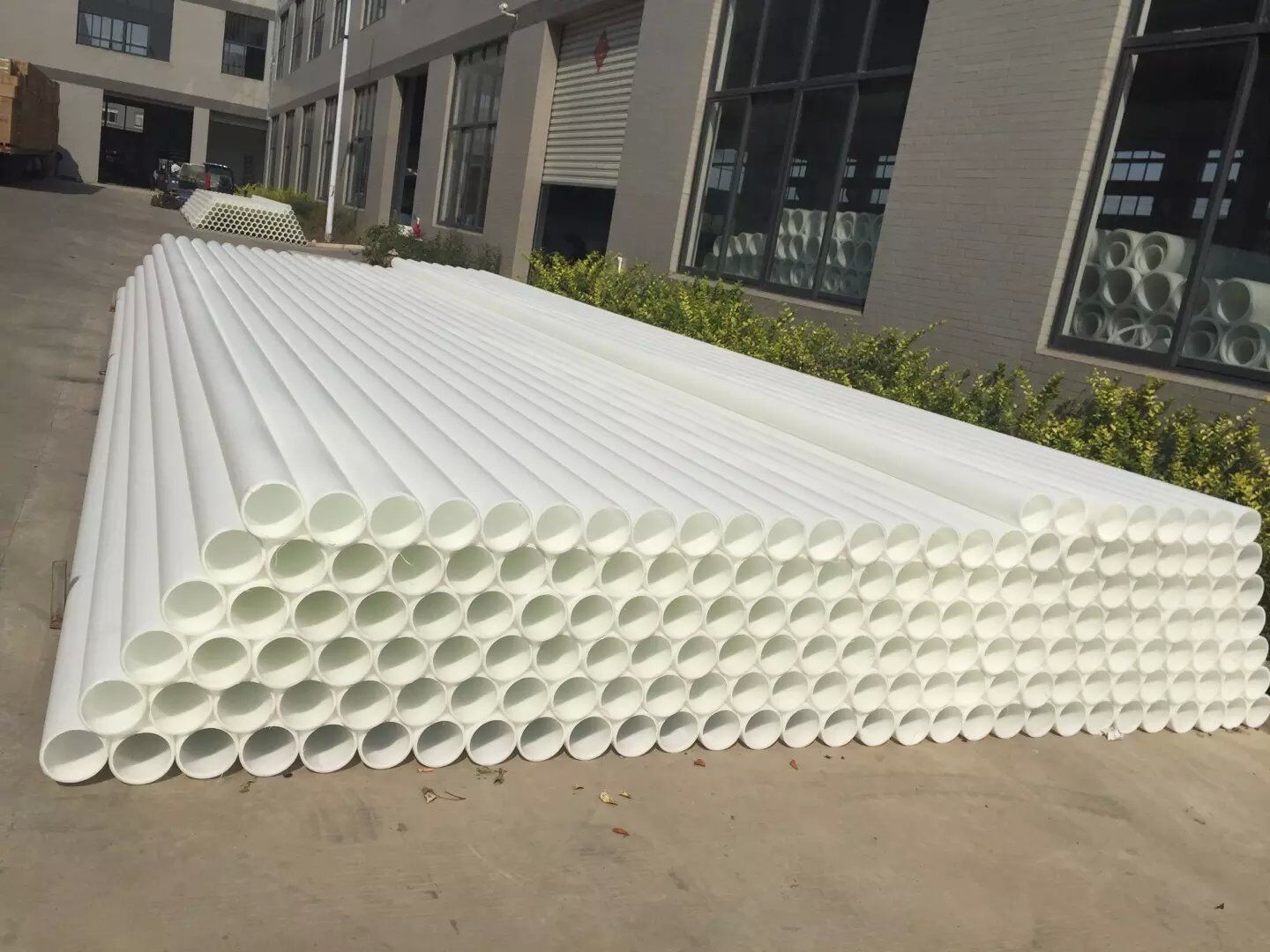
二、PPS塑料管注塑伸缩问题的正确解决策略
(一)***化材料选择与预处理
1. 选择合适的PPS牌号:不同的PPS牌号在分子结构、熔点、流动性以及收缩率等方面可能存在差异。根据具体的产品要求和注塑工艺条件,选择具有合适收缩率和******成型性能的PPS牌号是解决伸缩问题的***步。例如,对于一些对尺寸精度要求极高的PPS塑料管,可以选择收缩率较低且稳定的***种PPS牌号。
2. 材料预处理:在注塑前对PPS塑料进行干燥处理是非常重要的。由于PPS塑料容易吸湿,含水量过高会导致在注塑过程中产生气泡、银纹等缺陷,同时也会影响塑料的流动性和收缩率。一般将PPS塑料在120 150℃的温度下干燥3 4小时,使其含水量控制在合适的范围内,这样可以提高塑料的成型稳定性,减少因水分因素导致的伸缩问题。
(二)精准设计模具
1. ***计算型腔尺寸:根据所选PPS塑料的收缩率,***计算模具型腔的尺寸。通过实验测试或参考材料供应商提供的数据,确定在不同注塑工艺条件下PPS塑料的实际收缩率,并在模具设计时预留相应的收缩余量。例如,如果PPS塑料的收缩率为0.5% 0.7%,在设计型腔尺寸时,应将塑料管的尺寸放***相应比例,以确保冷却后的产品尺寸符合要求。同时,考虑到塑料管在不同方向上的收缩差异,对型腔的各个尺寸进行针对性的调整,以保证塑料管的整体尺寸精度。
2. ***化模具结构:合理设计浇口位置和数量,使塑料能够均匀地填充型腔,避免产生局部应力集中和流动不均匀的现象。一般来说,对于PPS塑料管,采用多点浇口或侧浇口的方式可以较***地实现塑料的均匀充模。此外,设计高效的冷却系统是解决伸缩问题的关键之一。采用循环水冷却或油冷却等方式,确保模具各个部位能够均匀冷却,减少塑料管不同部位的温度差异,从而降低收缩率的差异。例如,在模具型腔周围布置合理的冷却通道,使冷却介质能够充分接触模具表面,带走热量,实现均匀冷却。同时,还可以通过模拟仿真技术对模具的冷却效果进行***化,进一步提高冷却系统的设计精度。
(三)精细调控注塑工艺参数
1. 温度控制***化:根据PPS塑料的***性和产品要求,***控制熔体温度、模具温度和环境温度。一般来说,PPS塑料的熔体温度控制在280 320℃之间,模具温度控制在80 120℃之间较为合适。在实际生产中,通过安装温度传感器和温控装置,实时监测和调节温度,确保温度的稳定性。同时,对注塑机和模具进行保温措施,减少环境温度波动对注塑过程的影响。例如,在注塑机料筒周围包裹保温材料,在模具上安装加热和冷却装置,并根据环境温度的变化自动调整模具温度,以保证塑料管在稳定的温度条件下成型,减少伸缩变形。
2. 压力控制调整:合理设置注塑压力和保压压力,并根据塑料管的壁厚、长度以及形状等因素进行***化。一般来说,注塑压力控制在60 120MPa之间,保压压力为注塑压力的50% 80%,保压时间根据产品***小和厚度在5 20秒之间调整。在注塑过程中,通过压力传感器实时监测注塑压力和保压压力,并根据塑料的填充情况及时调整压力参数。例如,当塑料填充到型腔的80%左右时,适当降低注塑压力,以避免塑料在型腔内产生过***的剪切应力;在保压阶段,根据塑料的冷却情况逐步降低保压压力,防止塑料管内部产生缩孔和应力集中。
3. 注射速度和时间***化:根据PPS塑料的流动性和产品结构***点,选择合适的注射速度和时间。一般来说,注射速度控制在30 60mm/s之间,注射时间根据产品***小和厚度在2 10秒之间调整。在注塑过程中,通过调节注塑机的螺杆转速来控制注射速度,并通过实验确定***的注射时间和速度组合。例如,对于薄壁的PPS塑料管,可以适当提高注射速度,但要避免产生湍流和剪切应力;对于厚壁的塑料管,则应降低注射速度,延长注射时间,以确保塑料能够充分填充型腔并均匀冷却,减少伸缩变形的可能性。
(四)加强脱模与后处理控制
1. 脱模设计***化:设计合理的脱模机构,确保塑料管在脱模过程中不受损伤且能够顺利脱模。采用合适的脱模斜度,一般在0.5 1.5度之间,以减少塑料管在脱模时的摩擦力。同时,对模具表面进行抛光处理,降低表面粗糙度,使塑料管在脱模时能够顺畅滑动,避免因脱模困难而导致的伸缩变形。此外,还可以使用脱模剂来辅助脱模,但要注意脱模剂的选择和使用量,避免对塑料管的表面质量和性能产生不***影响。
2. 后处理工艺控制:注塑成型后的PPS塑料管需要进行适当的后处理,以进一步消除残余应力,提高尺寸稳定性。常用的后处理方法包括退火处理和调湿处理。退火处理是将塑料管在一定的温度下加热一段时间,然后缓慢冷却,使塑料内部的应力得到释放。一般来说,退火温度控制在玻璃化转变温度以上10 20℃,时间为1 2小时。调湿处理则是将塑料管放置在湿度较高的环境中一段时间,使其吸收一定量的水分,从而减少因干燥环境导致的水分流失而产生的收缩变形。通过合理控制后处理工艺参数,可以有效解决PPS塑料管的伸缩问题,提高产品的质量和性能。
PPS塑料管注塑伸缩问题的解决需要综合考虑材料***性、模具设计、注塑工艺以及脱模与后处理等多个环节。通过对这些方面的深入研究和***控制,可以有效地减少或消除PPS塑料管在注塑过程中的伸缩变形问题,提高产品的尺寸精度、外观质量和性能稳定性,满足不同工业***域对高性能塑料制品的需求。在实际生产过程中,生产企业应根据自身的设备条件、技术水平和产品质量要求,不断***化生产工艺和管理措施,持续改进产品质量,提升市场竞争力。